In the fast-paced world of industrial operations, ensuring compliance with environmental regulations is crucial. Enter LDARtools’ Chateau, a powerful LDAR monitoring software specifically designed to help organizations manage and streamline their inspection processes.
For environmental engineers, industrial compliance officers, and LDAR professionals, Chateau offers a seamless solution for maintaining regulatory compliance while enhancing operational efficiency.

The Importance of Chateau
Chateau is an innovative leap forward for LDAR monitoring software, especially with managing inspections in industrial settings. It provides an all-in-one platform for scheduling and conducting various inspections, ensuring compliance standards are met and environmental safety is prioritized. For professionals tasked with maintaining LDAR compliance, Chateau simplifies the intricate process of organizing inspections, allowing them to focus on what truly matters—safety and compliance.
Chateau’s user-friendly interface and robust features make it an indispensable tool for anyone in the industry. Whether you are an environmental engineer overseeing multiple sites, or a compliance officer ensuring adherence to regulations, Chateau offers the ability to schedule inspections with precision and access comprehensive data.
LDAR Compliance and Four Key Inspections
In the realm of Leak Detection and Repair (LDAR), four types of inspections stand out for their critical role in environmental safety and compliance, and are integral components of any comprehensive LDAR program: M21, Optical Gas Imaging (OGI), Audio Visual Olfactory (AVO), and Cooling Tower. Chateau helps manage each one of these types of inspections in ways no other LDAR monitoring software can.

M21 Inspections
M21 inspections are the backbone of LDAR programs, focusing on identifying and measuring gaseous emissions from equipment in industrial facilities. Compliance with Method 21 regulations ensures fugitive emissions are detected and controlled, minimizing their impact on the environment. Conducting regular M21 inspections is vital for maintaining air quality and preventing adverse health effects.
Optical Gas Imaging (OGI)
Optical Gas Imaging represents a leap forward in inspection technology, enabling professionals to visualize and identify gas leaks using infrared cameras. OGI inspections enhance the visibility of invisible gases, providing a powerful tool for detecting leaks that would otherwise go unnoticed. This technology is instrumental in reducing greenhouse gas emissions and supporting sustainable industrial practices.
Audio Visual Olfactory (AVO) Inspections
AVO inspections rely on the keen senses of inspectors to identify leaks through sight, sound, and smell. While simple conceptually, AVO inspections play a critical role in LDAR programs by providing an additional layer of detection. Trained inspectors use their expertise to spot anomalies, ensuring leaks are promptly addressed and environmental safety is upheld.
Cooling Tower Inspections
Cooling towers are essential components of many industrial facilities, responsible for dissipating excess heat. However, they can also be sources of fugitive emissions if not properly maintained. Regular inspections of cooling towers help identify issues such as leaks and inefficiencies, safeguarding environmental compliance and ensuring optimal performance.
Advantages of Using Chateau for Inspections
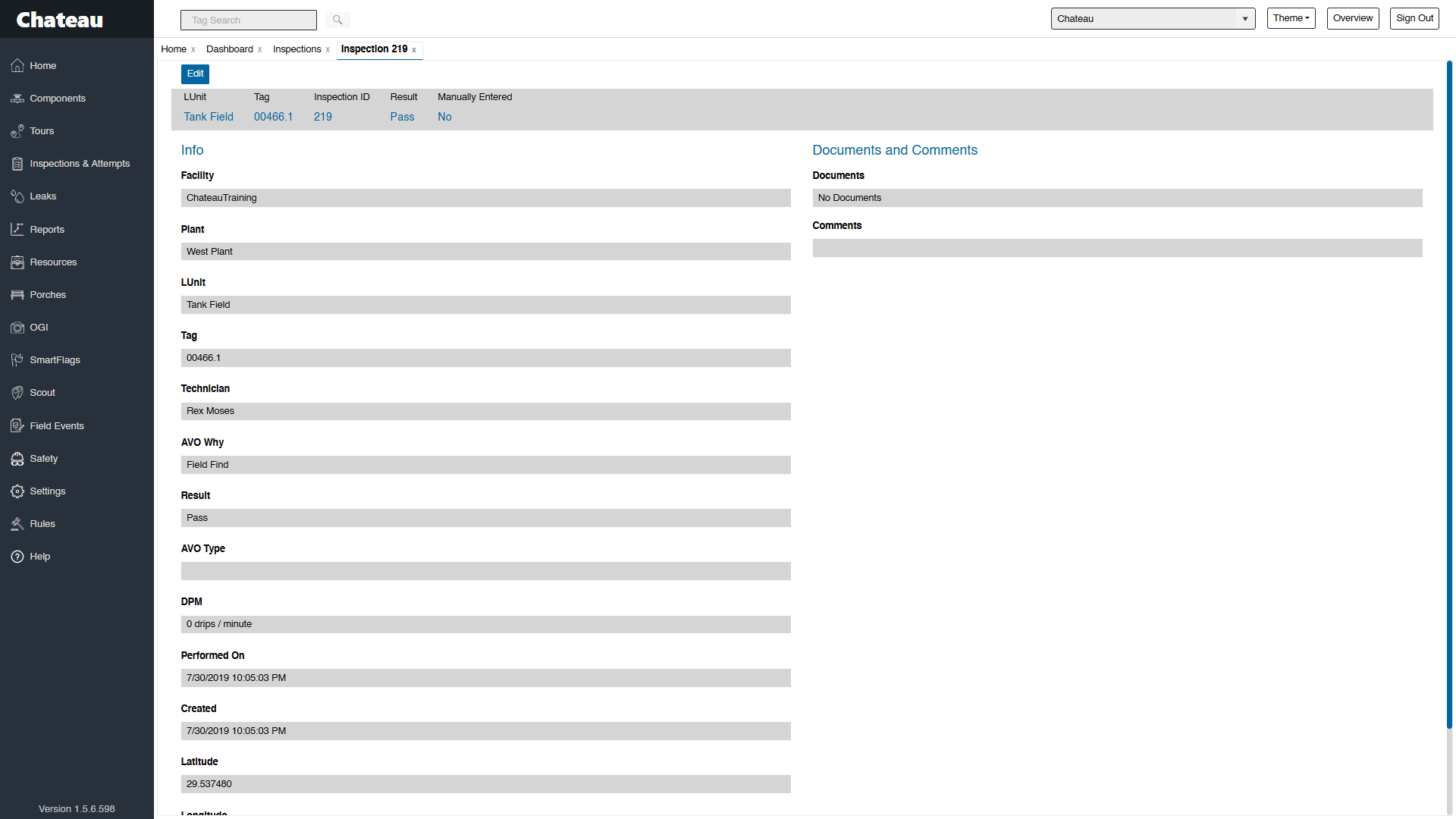
For environmental engineers, compliance officers, and safety professionals, the benefits of using Chateau LDAR monitoring software extend beyond scheduling and tracking inspections.
By automating the scheduling and management of inspections, Chateau reduces the administrative burden on professionals. This allows them to allocate more time to strategic tasks and decision-making. This efficiency translates into cost savings, as fewer resources are required to manage inspections and address compliance issues.
Additionally, Chateau’s centralized database ensures inspection data is accurate and easily accessible, eliminating the risk of data discrepancies and enhancing the reliability of compliance reporting. With accurate data at their fingertips, professionals can make informed decisions and implement effective corrective actions with Chateau better than any other LDAR monitoring software.
And finally, Chateau’s comprehensive tracking and reporting capabilities enable organizations to stay on top of compliance requirements. With real-time alerts and notifications, inspections are systematically conducted on schedule, reducing the risk of non-compliance and associated penalties.
Conclusion
LDARtools’ Chateau is a powerful LDAR monitoring software for mastering industrial inspections, offering a seamless solution for scheduling, conducting, and managing compliance efforts. By understanding the significance of M21, OGI, AVO, and Cooling Tower inspections, and leveraging Chateau’s capabilities, professionals can enhance environmental safety and operational efficiency.
Ready to take your inspection processes to the next level? Explore the benefits of Chateau and discover how it can transform your approach to LDAR compliance. Contact us today at sales@ldartools.com to learn more about the advantages of efficient scheduling, accurate data management, and improved compliance outcomes. Your path to streamlined inspections and environmental excellence starts here.